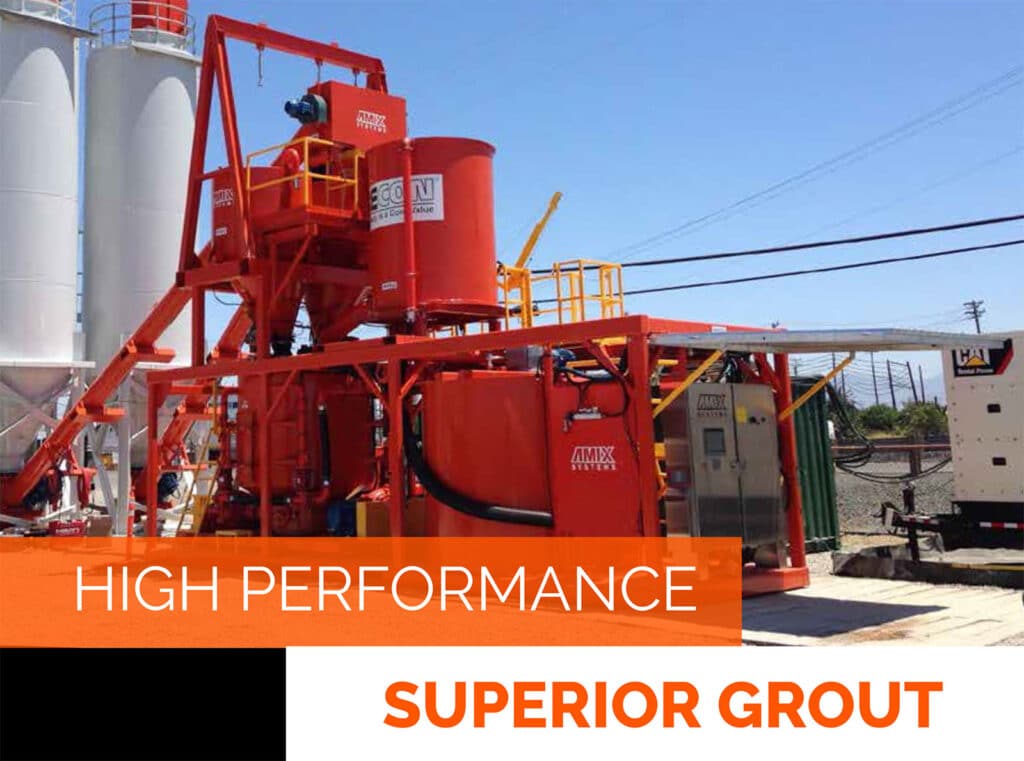
Book a discovery call with Ben MacDonald to learn how Amix Systems can transform your next project.
Grout Pumping Solutions for Mining Projects
Have you ever wondered what keeps massive underground mining operations stable or how tunneling projects maintain structural integrity beneath bustling North American cities? The answer often lies in sophisticated grout pumping systems that deliver precise material placement where conventional methods cannot reach. These specialized systems represent the backbone of modern construction and mining operations across Canada and the United States.
Grout pumping technology serves as a vital component in countless infrastructure projects, from subway tunnels beneath New York City to copper mines in British Columbia. The process involves transferring specially formulated grout mixtures through pressurized systems to fill voids, stabilize soil, and strengthen foundations in challenging environments. As construction projects become increasingly complex and mining operations extend deeper underground, the demand for reliable pumping solutions continues to grow throughout North America.
At Amix Systems, we understand the critical nature of grout pumping applications in demanding industrial environments. Our comprehensive range of slurry pumps and peristaltic pumps integrates seamlessly with automated mixing plants to provide complete grouting solutions. Contact our team to discuss how our proven pumping technology can optimize your next project’s performance and reliability.
This article will examine the technical aspects of modern grout pumping systems, their applications across various industries, and the innovations driving improved performance in North American construction and mining operations.
Understanding Modern Grout Pumping Technology
The evolution of grout pumping technology reflects the increasing complexity of modern construction and mining projects across North America. Traditional gravity-fed systems have given way to sophisticated pressurized pumping solutions capable of handling diverse material types and challenging placement scenarios. These advanced systems accommodate everything from fine cement slurries for precision grouting to high-density paste backfill materials used in underground mining operations.
Contemporary pumping systems must address multiple technical challenges simultaneously. Material handling requirements vary significantly between applications, with some projects requiring gentle handling of sensitive chemical grouts while others demand robust systems capable of moving abrasive materials through extended pipeline networks. The harsh operating environments common in North American mining and construction sites necessitate equipment designed for continuous operation under extreme conditions.
Automation has transformed grout pumping operations, reducing labor requirements while improving consistency and safety. Modern systems incorporate programmable controls that maintain optimal pressure and flow rates regardless of material variations or pipeline conditions. This technological advancement proves particularly valuable in remote mining locations where skilled operators may be limited and equipment reliability becomes paramount for project success.
Integration capabilities represent another crucial aspect of contemporary pumping technology. Today’s systems must interface seamlessly with mixing plants, material handling equipment, and project management systems to provide comprehensive grouting solutions. This integration enables real-time monitoring and adjustment capabilities that optimize performance while minimizing waste and downtime.
Applications Across Mining and Construction Industries
Mining Operations and Paste Backfill Systems
Underground mining operations throughout Canada and the United States rely heavily on grout pumping systems for paste backfill applications. These systems transport high-density mixtures of tailings, cement, and water into mined-out areas, providing structural support while enabling continued extraction activities. The challenging nature of underground environments demands pumping equipment capable of handling abrasive materials through complex pipeline networks over considerable distances.
Paste backfill operations require precise material handling to maintain optimal consistency and placement characteristics. The pumping systems must accommodate varying material properties while maintaining consistent flow rates and preventing segregation during transport. Underground conditions present additional challenges, including limited access for maintenance, extreme temperatures, and the need for continuous operation to support mining schedules.
Remote mining locations across northern Canada and Alaska present unique operational challenges for grout pumping systems. Equipment must function reliably in harsh weather conditions with minimal maintenance support. The integration of automated controls and self-cleaning technology becomes essential for maintaining operational continuity in these demanding environments.
Heavy Civil Construction and Infrastructure Projects
Large-scale infrastructure projects across North America utilize grout pumping systems for foundation stabilization, void filling, and ground improvement applications. Highway construction projects, bridge foundations, and urban development initiatives frequently require pumping systems capable of placing grout materials in precise locations under varying site conditions.
Tunneling projects represent some of the most demanding applications for grout pumping technology. Subway systems, highway tunnels, and utility corridors require specialized pumping solutions for annulus backfill, ground stabilization, and emergency grouting applications. The confined working spaces and continuous operation requirements typical of tunneling projects demand compact, reliable pumping systems with automated operation capabilities.
Environmental remediation projects increasingly rely on grout pumping systems for containment wall construction and groundwater control applications. These projects often require pumping systems capable of handling specialized grout formulations while maintaining strict environmental compliance standards mandated by EPA regulations and provincial authorities.
Technical Considerations for Grout Pumping Systems
Material Compatibility and Handling Requirements
Different grout formulations present unique pumping challenges that influence system selection and configuration. Cement-based grouts require systems capable of handling abrasive materials without excessive wear, while chemical grouts demand contamination-free handling to preserve material properties. The pumping system must accommodate these varying requirements while maintaining consistent performance across different applications.
Particle size distribution affects pumping performance significantly, particularly for systems handling materials with high solids content. Paste backfill applications typically involve materials with specific particle size requirements that influence pipeline design and pumping pressure calculations. Understanding these material characteristics enables proper system sizing and configuration for optimal performance.
Settling and segregation tendencies vary among different grout formulations, requiring pumping systems with appropriate agitation and circulation capabilities. Materials prone to settling demand continuous circulation or specialized handling techniques to maintain homogeneity during transport. The pumping system design must account for these characteristics to prevent blockages and ensure consistent material placement.
System Configuration and Integration Options
Pumping system configuration depends on project-specific requirements including material types, placement distances, and operational constraints. Centralized pumping stations offer advantages for high-volume applications, while distributed systems provide flexibility for projects with multiple placement locations. The choice between these configurations affects equipment selection, pipeline design, and operational procedures.
Integration with mixing plants requires careful consideration of material handling workflows and control system compatibility. Automated systems can coordinate mixing and pumping operations to optimize material properties and minimize waste. This integration becomes particularly important for applications requiring precise timing and material consistency.
Pipeline design considerations include material compatibility, pressure ratings, and cleaning requirements. Different grout formulations may require specific pipeline materials or configurations to prevent contamination or excessive wear. The pipeline system must accommodate cleaning procedures necessary for material changeovers or extended shutdown periods.
Comparison of Grout Pumping Technologies
Technology Type | Material Handling | Pressure Capability | Maintenance Requirements | Application Suitability |
---|---|---|---|---|
Centrifugal Slurry Pumps | Abrasive materials, high-density slurries | High pressure, variable flow | Replaceable wear components | Mining, heavy civil construction |
Peristaltic Pumps | Gentle handling, contamination-free | Moderate pressure, precise flow | Replaceable tubing elements | Chemical grouting, precision applications |
Progressive Cavity Pumps | Consistent flow, minimal pulsation | Moderate to high pressure | Regular maintenance required | Continuous operation, paste materials |
Diaphragm Pumps | Versatile material handling | Variable pressure capability | Diaphragm replacement needed | General grouting, material transfer |
This comparison illustrates how different grout pumping technologies address specific operational requirements across various applications. The selection process must consider material characteristics, performance requirements, and operational constraints to identify the optimal solution for each project.
Amix Systems Grout Pumping Solutions
Our comprehensive approach to grout pumping combines proven technology with innovative design to address the demanding requirements of North American mining and construction operations. We offer both high-performance slurry pumps and precision peristaltic pumps, each engineered to excel in specific applications while maintaining the reliability required for continuous industrial operation.
Our slurry pump designs feature robust construction with replaceable wear components that maximize uptime while minimizing long-term operating costs. These systems handle the most challenging materials, including abrasive paste backfill mixtures and high-density grouts used in mining applications. The modular design enables customization for specific project requirements while maintaining proven performance characteristics.
Peristaltic pump systems provide precise flow control and contamination-free operation for specialized applications requiring accuracy and material integrity. These systems excel in chemical grouting applications and precision dosing requirements where material purity and accurate flow rates are paramount. The self-priming capability and variable speed controls offer operational flexibility across diverse application requirements.
Integration capabilities represent a key strength of our pumping solutions. Our systems interface seamlessly with our complete range of colloidal mixing plants, from Typhoon series units for smaller applications to Hurricane series plants for high-volume operations. This integration enables automated operation and real-time monitoring that optimizes performance while reducing labor requirements.
We provide comprehensive support throughout the project lifecycle, from initial system design and configuration through commissioning and ongoing maintenance support. Our experience across diverse applications enables us to recommend optimal configurations that balance performance requirements with operational constraints. Contact our technical team to discuss how our grout pumping solutions can address your specific project requirements.
Future Trends and Operational Best Practices
The advancement of grout pumping technology continues to focus on automation, reliability, and environmental responsibility. Remote monitoring capabilities enable operators to oversee multiple pumping operations from centralized control rooms, improving efficiency while reducing on-site labor requirements. These systems provide real-time performance data that enables predictive maintenance and operational optimization.
Smart sensor technology integration offers enhanced monitoring capabilities that detect potential issues before they impact operations. Pressure sensors, flow meters, and material property monitors provide continuous feedback that enables automatic adjustments to maintain optimal performance. This technology proves particularly valuable for remote operations where immediate response to changing conditions is essential.
Environmental considerations increasingly influence pumping system design and operation. Energy-efficient motors, reduced noise operation, and improved containment systems address growing environmental awareness in the construction and mining industries. These improvements align with corporate sustainability goals while maintaining the performance required for demanding applications.
Best practices for grout pumping operations emphasize proper system maintenance, operator training, and quality control procedures. Regular inspection and maintenance of wear components prevents unexpected failures that can disrupt project schedules. Comprehensive operator training ensures safe and efficient system operation while maximizing equipment lifespan.
Material testing and quality control procedures verify grout properties throughout the pumping process, ensuring placement specifications are met consistently. These procedures become particularly important for applications where material properties directly affect structural performance or regulatory compliance.
Conclusion
Grout pumping technology continues to play an essential role in supporting North American construction and mining operations, from urban infrastructure projects to remote mining facilities. The evolution toward automated, reliable systems addresses the growing complexity of modern projects while improving operational efficiency and safety. Understanding the technical considerations and application requirements enables proper system selection that optimizes project performance.
As projects become more demanding and environmental standards more stringent, the importance of proven grout pumping solutions becomes increasingly apparent. The integration of advanced pumping systems with comprehensive mixing and material handling equipment provides the reliability and performance required for successful project completion.
Consider these questions as you evaluate grout pumping solutions for your operations: How can automated pumping systems improve your project efficiency while reducing operational risks? What role does equipment reliability play in your project scheduling and cost management? How might integrated grouting solutions address your specific application challenges while meeting environmental compliance requirements?
Contact Amix Systems today to discuss how our proven grout pumping solutions can optimize your next project’s performance. Our experienced team can assess your specific requirements and recommend systems that deliver the reliability and efficiency your operations demand.
Book A Discovery Call
Empower your projects with efficient mixing solutions that enable scalable and consistent results for even the largest tasks. Book a discovery call with Ben MacDonald to discuss how we can add value to your project:
Email: info@amixsystems.com – Phone: 1-604-746-0555
Postal Address: Suite 460 – 688 West Hastings St, Vancvouver, BC. V6B 1P1